Please note that all containers are within spec but the process is clearly not in control. Instead it drifts to the upper and lower boundary. The out of control range on subgroup 6 could indicate that there is a problem with one parison or there is a problem with extruder surging, inconsistent material mix or the like. As you can see from this chart, it is not enough to look at the cpk value. This value is high because the process mean is very close to the middle of the specification limits and therefore the calculations pan out to a high value.
Let's look at a similar process with the weights closer to the lower limit:
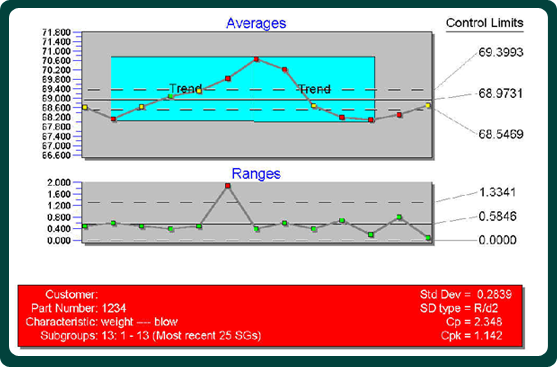
All containers are still within spec and the ranges are very similar. The cpk value is only half of the previous example because the values are now closer to the lower limit.
It becomes apparent from these charts that our initial parameters need to be close to the middle of the specification limits because we have a bigger process window to work with and can produce containers within spec even when our machine capabilities are not 100%.
A number of subgroups where one subgroup has a continuously higher (or lower) mean, can be called a trend. This feature allows QC personnel to alert the operator to a potential problem that could lead to out of spec samples. The operator can then make an adjustment or at least watch the process more closely. In any case, a chart like the two above should lead to an investigation and the underlying problem should be addressed.
Next month we will look at a Design of Experiment to find the cause of the weight fluctuations.